Critical success factors. The country’s industrial sector is well-known for its cutting-edge technology, highly skilled workforce, and commitment to continuous improvement. One of the most important measures in this efficiency drive is cycle time, which is the overall time required to accomplish a single unit of output. Understanding and optimizing cycle time enables firms to boost output, reduce costs, and better meet consumer demands. Given Singapore’s reputation for operational efficiency, understanding cycle time management is crucial for companies seeking to remain competitive in a rapidly changing market.
In this post, we will look at the many components of cycle time, how they affect manufacturing processes, and how to improve them. According to YCP, the adoption of Industry 4.0 technologies in Singapore’s industrial sector will result in an additional USD 26 billion in output by 2024. This rise is mostly driven by greater operational efficiencies, such as shorter cycle times, made possible by technology such as automation and data analytics. This data emphasizes the need of optimising cycle time in order to increase production and sustain competitiveness in Singapore’s changing industrial scene.
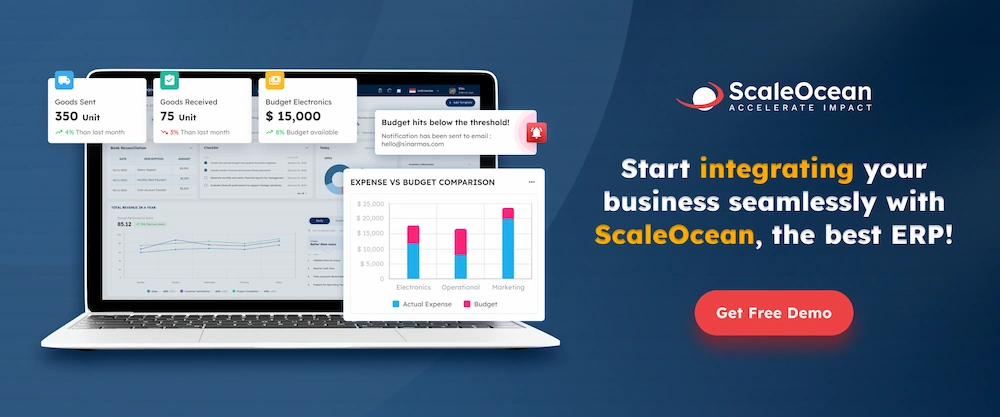
1. What Is Cycle Time?
Cycle time is the overall time it takes to perform a manufacturing activity for a single unit or batch, from when production begins to when it ends. This comprises each phase of the process, such as preparation, processing, waiting, and transportation. It is an important statistic for determining a production system’s efficiency because it has a direct impact on output, resource allocation and overall performance. By monitoring cycle time, manufacturers can discover bottlenecks, optimize operations, and increase throughput.
A manufacturing execution system Singapore can help with this process by providing real-time data tracking and improved resource management. Essentially, cycle time is a key indicator for organizations seeking to optimize their manufacturing processes, reduce delays, and meet production targets effectively. Understanding and reducing cycle time can lead to faster production cycles, cheaper costs, and greater market competitiveness. The components of cycle time are key elements that contribute to the total time required to complete a manufacturing process. These include:
a. Processing Time
This refers to the time spent actively working on the product, adding value through procedures such as assembling, machining, and painting. It is the point at which the product is physically transformed or completed during the manufacturing process. Efficient processing time increases throughput while also ensuring that resources are used effectively.
b. Waiting Time
This is the time when the product sits idle, waiting for the next stage in the manufacturing process or for supplies, tools, or approvals. Waiting time can be caused by operational delays, and excessive waiting can reduce output, resulting in inefficiencies. Reducing wait time is critical to decreasing overall cycle time.
c. Transport Time
This refers to the time spent transferring the product between workstations or departments. Transport time, whether moving raw materials to the assembly line or finished products to the packing area, can be a hidden cost in the manufacturing process. Minimizing needless movement and optimizing layout can save transport time, resulting in smoother operations and shorter cycle times.
Also Read: What is Mass Production? Benefits, Challenges, and Examples
2. Types of Cycle Time
There are two variations of cycle time, each offering a distinct perspective on manufacturing efficiency. Understanding these categories enables manufacturers to target specific areas for performance optimization. Businesses that analyze different cycle periods might enhance resource allocation and streamline production operations. There are various variations of cycle time, each offering a distinct perspective on production efficiency:
a. Effective Cycle Time
This category encompasses all actions that contribute to the production process, not only direct manufacturing procedures. It includes duties such as loading and unloading materials, setup time, and any other acts that contribute to the entire process. It provides a larger picture of the manufacturing process and its efficiency, assisting in the identification of any additional delays that may impair overall performance.
b. Equipment Cycle Time
Equipment Cycle Time is the time spent actively processing one unit of manufacture, excluding preliminary or finishing procedures. It focuses on the time when equipment is actively producing a product. According to Trading Economics, machinery and transport equipment accounted for 61.48% of the value added in Singapore’s manufacturing sector in 2022, emphasizing the significance of effective equipment operation. Optimizing equipment cycle time enables manufacturers to boost productivity, cut costs, and improve competitiveness in Singapore’s continuously changing industrial scene.
3. Why Is Cycle Time Important?
Cycle time is critical to assessing the efficiency and profitability of industrial processes. Businesses that constantly monitor and manage cycle time can find opportunities for improvement and guarantee that their manufacturing lines run smoothly. Reducing cycle time improves not just internal procedures, but also customer satisfaction and competitiveness.
a. Operational Efficiency
Shorter cycle times enable producers to complete more units in a given time frame, hence considerably increasing production capacity. This indicates that machines and manpower are being used more efficiently, resulting in shorter idle times and improved workflow. Businesses can enhance the entire flow of operations by lowering the time spent on each unit, resulting in speedier product production while maintaining quality requirements.
b. Cost Reduction
Optimizing cycle time lowers labor expenses by reducing the amount of time employees spend on each task. It also reduces operational costs by ensuring that equipment is used as efficiently as possible, preventing unnecessary downtime. The faster the production process, the less money is spent on utilities, maintenance, and other operational costs, ultimately impacting the cost of goods sold. By optimizing these expenses, businesses can improve profitability while maintaining competitive pricing.
c. Customer Satisfaction
Faster production timelines mean a shorter turnaround from order to delivery, which directly enhances customer satisfaction. Customers feel cherished when things arrive on time or ahead of schedule, and they are more inclined to return for future purchases. Furthermore, shorter cycle times allow manufacturers to better respond to changing client expectations, ensuring that companies can quickly adjust to variations in market needs.
4. How to Calculate Cycle Time
The cycle time computation is straightforward and can be accomplished using a simple formula. Understanding this computation allows manufacturers to analyze production efficiency and find areas for improvement. Businesses that track cycle time may calculate how long it takes to produce each item, which is critical for optimizing operations. This enables for more effective planning and resource allocation, ultimately enhancing the production process. The following is the formula for cycle time:
Cycle Time = Process Duration / Total Units Produced
For example, if a machine produces 90 units in one hour (60 minutes), the cycle time can be calculated as: 60 minutes / 90 units equals 0.67 minutes per unit. This indicates that each unit takes approximately 0.67 minutes to generate. Monitoring this number allows producers to analyze performance, find inefficiencies, and make modifications to increase productivity and minimize lead times.
5. What Is Cycle Time Loss?
Cycle time loss happens when production processes diverge from their optimal speeds, resulting in delays and inefficiencies. This can occur as a result of equipment operating below its maximum capacity or tiny halt during production that are not technically classified as downtime, such as brief interruptions or machine slowdowns. These little inefficiencies add up over time, resulting in longer production cycles and higher prices.
Addressing cycle time loss is critical to ensuring a smooth and cost-effective production process. Manufacturers can take corrective action by identifying the root causes, which may include equipment faults, process inefficiencies, or human mistake. Regular maintenance, process improvement, and continual monitoring of operations can assist reduce cycle time loss, keeping production on track and prices low.
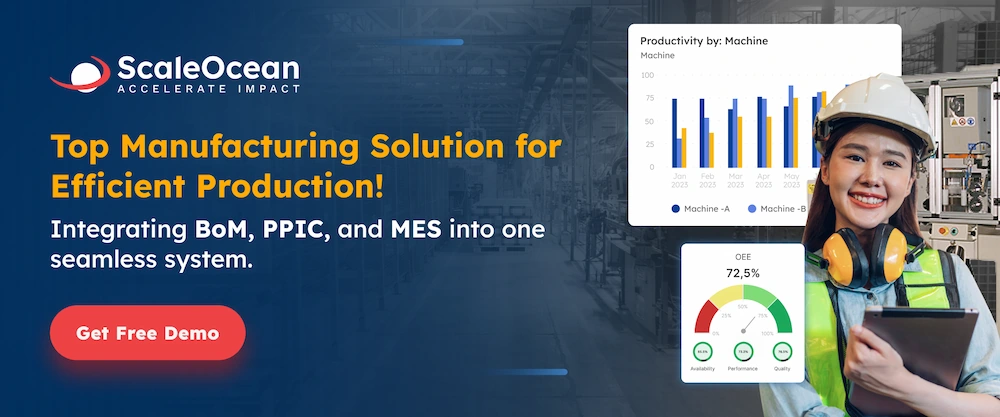
6. Causes of Cycle Time Loss
Several variables contribute to cycle time loss, which results in inefficiencies that can affect overall production. Identifying and treating these factors is critical for streamlining manufacturing processes and increasing operational efficiency. Understanding the underlying causes allows manufacturers to apply measures to reduce delays and cycle time loss. The following are the main causes of cycle time loss:
a. Equipment Downtime
Machines may cease working due to breakdowns or maintenance concerns, momentarily halting production. Even minor disruptions in equipment operation can cause large delays since repair times and modifications add to the overall cycle duration. Regular maintenance schedules and quick response teams can assist reduce downtime and keep operations running smoothly.
b. Inefficient Processes
Unnecessary steps or delays in the workflow can increase the time required to perform jobs. Inefficiencies, such as redundant processes, manual handling, and stage delays, accumulate over time and have a negative impact on cycle time. Streamlining operations, removing bottlenecks, and automating specific tasks can all assist to reduce delays.
c. Material Shortages
Delays caused by a lack of required materials might halt production or force workers to wait for supplies to arrive. Insufficient inventory management or supply chain disruptions can lead to idle time and longer cycle durations. Maintaining good inventory management and cultivating excellent supplier connections can assist alleviate shortages and prevent production delays.
Also Read: What is Material Requirement Planning (MRP) and Its Benefits
7. How to Reduce Cycle Times
Reducing cycle durations necessitates targeted tactics for maximizing production and overall efficiency. Businesses may create smoother, faster production cycles by identifying key areas for saving time and improving procedures. These tactics aid not just in increasing speed, but also in lowering expenses and expanding capacity. The following are the main techniques of reduce cycle times:
a. Process Optimization
Streamlining workflows entails eliminating redundant procedures that do not add value to the end product. Manufacturers can improve their workflows by assessing the entire production process and finding bottlenecks or unnecessary processes. To reduce delays and boost speed, certain processes may be automated, the production layout reorganized, or manual handling eliminated.
b. Preventive Maintenance
Regular maintenance ensures that equipment performs optimally, lowering the likelihood of breakdowns or malfunctions. Scheduled inspections and prompt repairs aid in detecting possible problems before they create major downtime. By properly maintaining equipment, producers may avoid unexpected disruptions and keep production operating smoothly, thus saving cycle time.
c. Employee Training
Well-trained staff are more efficient and make fewer mistakes, resulting in shorter cycle times. Ensuring that staff have the necessary skills and knowledge to complete their tasks correctly and quickly can help to reduce delays. Regular training programs and continuing skill development can help personnel manage their tasks more effectively, resulting in speedier and smoother production processes.
8. Example of Cycle Time Calculation
Consider a bakery that bakes a batch of bread in 30 minutes with a total of 60 loaves. To figure how long it takes to bake each individual loaf, divide the batch’s total duration by the number of loaves produced. In this scenario, the batch lasts 30 minutes and consists of 60 loaves. So, the cycle time per loaf is:
Cycle Time per Loaf = 30 minutes / 60 loaves = 0.5 minutes per loaf.
This means that each loaf of bread bakes for 0.5 minutes (or 30 seconds). Understanding cycle time enables the bakery to evaluate its production process, determine whether it is working efficiently, and discover areas for improvement, such as improving the baking process or adjusting batch size to better meet demand.
9. Cycle Time in Manufacturing ERP Software
Manufacturing ERP software is critical for monitoring and optimizing cycle times throughout the production process. Businesses that integrate ERP systems into their production workflows get the ability to analyze cycle times in real time, allowing them to identify bottlenecks or inefficiencies as they occur. This real-time data enables immediate changes to optimize flow, eliminate delays, and avoid downtime.
In addition to cycle time tracking, ERP systems provide a number of other significant advantages that increase overall production performance. They improve scheduling by providing correct information about when tasks are completed and when resources are accessible. ERP systems also optimize resource allocation, ensuring that machines, personnel, and materials are used effectively. These skills ultimately result in increased production efficiency, ensuring that orders are fulfilled on time and with greater precision, while also lowering costs and boosting overall operational performance.
10. Cycle Time vs. Throughput Time vs. Takt Time
While cycle time indicates the time it takes to finish one unit, there are other terms that offer context and assist manufacturers better understand their production flow. These terms—throughput time and takt time—are complementing measurements that provide a more complete picture of production efficiency and meeting customer demand. By comparing these three measures, manufacturers can find areas for improvement and make informed decisions about how to optimize their processes.
a. Cycle Time
This is the time necessary to produce a single unit. It assesses the efficiency of a single operation or workstation and is critical for finding bottlenecks or areas that can be improved in the manufacturing process. A shorter cycle time translates into a higher production rate, which leads to increased capacity and output.
b. Throughput Time
This is the overall time a product spends throughout the complete manufacturing process, from start to finish. It includes not just the processing time, but also the waiting time, travel time, and other delays that may arise along the way. Reducing throughput time entails minimizing delays between activities, which speeds up the entire production process.
c. Takt Time
Takt time refers to the rate at which things must be manufactured to meet customer demand. It helps to align production speed with demand, ensuring that products are produced at the appropriate rate to avoid overproduction or underproduction. Takt time is computed by dividing available production time by customer demand rate, allowing producers to manage production capacity and demand.
Also Read: What is Production Efficiency and How to Calculate It?
11. How to Improve Cycle Time
Improving cycle time entails implementing numerous solutions targeted at increasing manufacturing efficiency and reducing production delays. Businesses that focus on waste elimination, process refinement, and the use of sophisticated technology can drastically reduce cycle times and enhance productivity. These tactics not only improve operations, but also help to maintain high product quality and meet client expectations more effectively. The following are significant ways for improving cycle time:
a. Lean Manufacturing
Lean manufacturing focuses on minimizing waste throughout the production process, including unnecessary motions, overproduction, and excess inventory. By streamlining workflows and optimizing resource utilization, lean concepts help improve efficiency, ultimately leading to shorter cycle times. This approach enhances the overall production process by ensuring that every step adds value and reducing time spent on non-essential activities. The strategy promotes continual waste reduction, resulting in faster production times and cheaper costs.
b. Continuous Improvement
Regularly reviewing and refining processes enables firms to uncover inefficiencies and opportunities for improvement. This can include minor modifications, such as reorganizing workstations, or more significant ones, such as automating specific jobs. Manufacturers can lower cycle times and enhance overall efficiency by cultivating a culture of continuous improvement.
c. Technology Adoption
Implementing automation and modern manufacturing technology, such as robotics and machine intelligence, can greatly improve operations. These technologies aid in the reduction of manual labor, the reduction of human error, and the acceleration of repeated activities, all of which contribute to shorter cycle times. Manufacturers may improve the agility and efficiency of their production environments by investing in the proper tools and technologies, including manufacturing cost estimating software, which can help predict and control production costs more effectively.
12. Enhance Your Manufacturing Efficiency with ScaleOcean’s ERP Solutions
ScaleOcean is a leading ERP provider for the manufacturing industry, offering a solution with over 200 specialized modules and 1000+ functionalities. It integrates seamlessly with IIOT for real-time data, automated workflows, and reduced manual involvement, leading to lower costs, increased productivity, and scalable growth. Businesses adopting ScaleOcean may also benefit from CTC (Critical Technology Cluster) grants to reduce implementation costs.
ScaleOcean’s ERP solutions can help you realize the full potential of your industrial processes. By participating in our free demo, you can take the first step toward greater efficiency and long-term success. This is a great opportunity to learn how ScaleOcean can help you optimize your production processes and boost your business performance. Don’t miss out on the chance to discover firsthand how our innovative technology can help you succeed, all while benefiting from the support of CTC grants. The following are the key features of ScaleOcean’s software:
- All-in-One Solution – Comprehensive Modules Tailored to Your Needs, ScaleOcean offers 200+ specialized modules and 1000+ specific features to meet the diverse needs of your manufacturing business.
- Built on Best Business & Industry Practices, Our ERP system is built on industry best practices, providing solutions to tackle operational challenges, improve efficiency, and automate workflows.
- Industrial Internet of Things (IIOT) Integration, ScaleOcean integrates seamlessly with IIOT, offering a 360° view of your manufacturing processes. Real-time data from connected devices ensures better decision-making and operational transparency.
- Auto-Pilot for All Business Operations, Our system is designed with advanced automation features tailored to your workflow. From production scheduling to inventory management, ScaleOcean ensures your operations run smoothly with minimal manual intervention.
- Customizable Platform Integration, ScaleOcean allows easy integration with other platforms your company already uses. This ensures a unified system that enhances efficiency and reduces the complexity of managing multiple tools.
13. Conclusion
Understanding and optimizing cycle time is critical to increasing manufacturing efficiency and remaining competitive in today’s fast-paced market. Throughout this essay, we have looked at the significance of cycle time, its numerous components, and how it can be calculated and improved. Manufacturers can streamline their processes, reduce manufacturing costs, and boost overall productivity by addressing the causes of cycle time loss. The integration of modern ERP systems, such as ScaleOcean, is critical for tracking, managing, and improving cycle time throughout the production process.
We welcome you to test a free demo of ScaleOcean’s ERP systems to see how they might improve your manufacturing operations. Learn firsthand how our sophisticated features, such as real-time tracking and predictive analytics, may help you improve cycle time, resource management, and long-term growth. ScaleOcean’s cutting-edge technology can help you improve your business’s efficiency right now.