Understanding manufacturing overhead is important for any company involved in production. While direct expenses such as raw materials and labor are easy to calculate, overhead costs are frequently overlooked, despite playing an important role in determining the true cost of goods. Manufacturing overhead refers to the indirect expenses required to run the manufacturing process, such as factory rent, utilities, and maintenance.
These costs cannot be directly attributed to any single product, but they are required for the production process to function properly. Understanding how to calculate manufacturing overhead is essential for accurate pricing, budgeting, and profit. In this post, we will explain manufacturing overhead and walk you through the steps to accurately calculate it for your company.
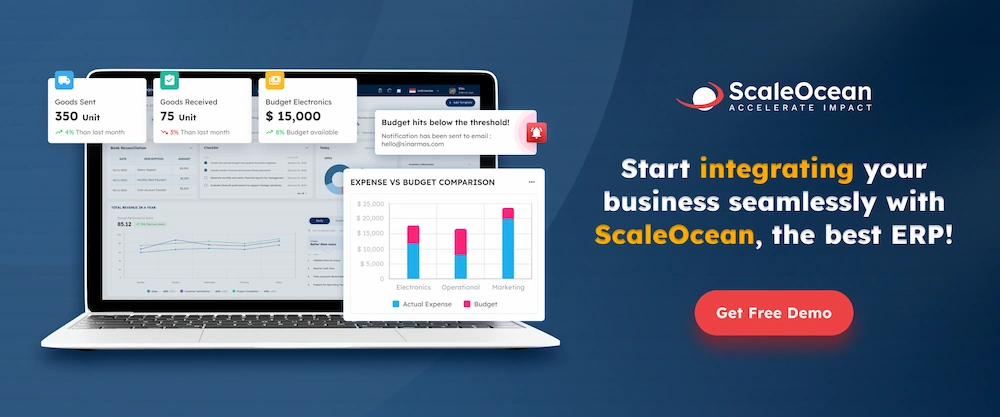
What is the Manufacturing Overhead?
Manufacturing overhead is the total of all indirect costs connected with producing a product. These expenses are necessary for running a manufacturing plant, even if they are not directly related to the production of something specific. Overhead costs include rent, utilities, depreciation, equipment maintenance, and support staff salaries.
Managing these expenses effectively helps businesses maintain profitability and operational efficiency. Companies allocate overhead costs using machine hours or labor hours to ensure accurate product pricing. Without proper overhead management, businesses may experience financial inefficiencies that affect their bottom line. Tracking and optimizing these costs are essential for long-term manufacturing operations.
What is Included in Manufacturing Software?
Manufacturing overhead includes indirect costs required to operate a production operation. These costs are useful for supporting industrial operations, though not directly related to producing individual items. Properly tracking and managing these overhead expenses is vital for accurate pricing, cost efficiency, and profitability. Here are the main components of manufacturing overhead.
1. Facility Rent
Facility rent covers the cost of leasing or renting the manufacturing site. This cost is a fixed overhead expense that businesses must pay consistently, within all manufacturing levels, such as mass production. A carefully negotiated lease agreement enables manufacturers to manage costs effectively and maintain financial stability while securing an ideal location for production operations.
2. Utility Costs
Utility costs include power, gas, water, and waste disposal, which are required to keep production operations going properly. These expenses fluctuate based on operational intensity and seasonal variations. Monitoring and optimizing utility consumption through energy-efficient practices can help manufacturers reduce costs and improve sustainability.
3. Equipment Maintenance
Regular maintenance ensures that manufacturing machinery operates efficiently, reducing downtime and costly breakdowns. This includes scheduled maintenance, emergency repairs, and the replacement of worn-out components. Preventative maintenance procedures help to extend equipment life, increase productivity, and reduce unexpected production disruptions.
4. Asset Depreciation
Manufacturing equipment, buildings, and vehicles lose value over time as a result of wear and tear. Asset depreciation is an accounting charge that reflects this loss of value. Proper depreciation tracking helps manufacturers to make more informed decisions about equipment replacement, tax breaks, and long-term financial planning.
5. Workforce Expenses
Manufacturing overhead includes wages for factory staff who do not directly produce goods, such as supervisors, janitors, and maintenance personnel. These employees contribute to operational efficiency by ensuring smooth workflow, maintaining cleanliness, and supporting production teams. Managing labor costs effectively enhances productivity and cost control.
6. Operational Supplies
General-use items such as cleaning materials, lubricants, and protective gear fall under operational supplies. While not directly tied to specific products, these supplies are essential for maintaining a safe and efficient production environment. Monitoring supply usage and optimizing procurement strategies help reduce unnecessary spending.
7. Insurance Premiums
Manufacturing plants need insurance to cover risks like property damage, liability claims, and equipment breakdowns. Paying for insurance is a key overhead cost that protects business assets and ensures financial stability during unexpected events. Selecting the right insurance policies helps reduce risks and manage expenses.
8. Tax Obligations
Manufacturers must pay property taxes and other levies on their facilities and equipment. These tax obligations vary based on location and regulations. Proper tax planning and compliance help businesses avoid penalties, optimize financial strategies, and ensure uninterrupted operations while maintaining legal obligations.
9. Professional Fees
Legal, accounting, and consulting services required for business operations are all included in professional fees. These costs are necessary to ensure compliance with financial regulations, labor laws, and industry standards. Using qualified professionals allows manufacturers to streamline processes, reduce risks, and improve overall business efficiency.
Also read: Top 8 Manufacturing Execution System in Singapore 2025
Manufacturing Overhead Formula
The manufacturing overhead formula calculates the indirect costs of production that are not directly tied to materials or labor. By accurately determining these costs, businesses can ensure more precise manufacturing cost estimation and allocation, ultimately leading to better pricing strategies and improved financial management. The formula is:
Manufacturing Overhead = Indirect Materials + Indirect Labor + Other Overhead Costs
Indirect materials include supplies used in production but not part of the final product, such as lubricants and cleaning supplies. Indirect labor consists of wages for workers not directly involved in production, like supervisors and maintenance staff. Other overhead costs encompass utilities, depreciation, rent, insurance, and factory maintenance. This formula helps businesses determine the total indirect costs necessary to run a manufacturing process efficiently.
How to Calculate Manufacturing Overhead
Calculating manufacturing overhead involves identifying all indirect costs related to production, summing them up, and applying them to products based on a predetermined rate. This helps businesses understand total production costs and set accurate prices.
Start by listing all indirect costs, which may include expenses like factory rent, utilities, equipment depreciation, maintenance, and indirect labor. Next, sum all these overhead expenses for a specific period, whether it’s monthly, quarterly, or annually. Then, determine the allocation base to distribute the overhead costs, selecting from options such as labor hours, machine hours, or production units. After that, calculate the overhead rate using the formula below.
Overhead Rate =
Total Allocation Base / Total Manufacturing Overhead
For instance, if overhead costs are $50,000 and total labor hours are 10,000, the rate is $5 per labor hour. Lastly, multiply the overhead rate by the allocation base for each product to estimate its share of indirect costs.
Also read: What is Material Requirement Planning (MRP) and Its Benefits
How is Manufacturing Overhead Used?
Manufacturing overhead is important to cost management, pricing, and profitability. It includes indirect production costs such as rent, utilities, and maintenance, which ensure accurate financial reporting, cost allocation, and manufacturing efficiency. Understanding its applications enables businesses to reduce costs and maintain competitive pricing in the market.
1. Cost Allocation for Accurate Pricing
Manufacturing overhead is distributed across products to determine their true production cost. This helps businesses set competitive yet profitable prices by ensuring all indirect costs are factored in. Without proper allocation, products may be underpriced or overpriced which affects overall profitability.
2. Financial Reporting and Compliance
Accurate tracking of manufacturing overhead is important for financial statements and tax compliance. Companies must report indirect costs correctly to meet accounting standards and regulatory requirements. Proper overhead accounting ensures transparency, helping businesses make informed financial decisions and avoid discrepancies in audits or financial evaluations.
3. Budgeting and Cost Control
Manufacturing overhead analysis helps businesses identify areas where costs can be reduced without impacting quality. By monitoring expenses like utilities, equipment depreciation, and maintenance, manufacturers can optimize their budgets, enhance efficiency, and allocate resources effectively to maximize profitability while keeping production costs under control.
4. Production Efficiency and Process Improvement
Tracking overhead costs reveals inefficiencies in manufacturing operations. Businesses can use these expenses to streamline processes, reduce waste, and optimize resource utilization. For example, high energy costs may indicate inefficient machinery, requiring investments in energy-saving equipment to reduce long-term production costs and improve overall efficiency.
5. Decision-Making in Manufacturing Strategy
Manufacturing overhead data supports strategic decisions such as pricing changes, process automation, and facility expansions. Companies can use cost trends to decide whether to outsource production, invest in new technology, or optimize workforce planning. These insights ensure long-term growth and competitiveness in an ever-changing manufacturing landscape.
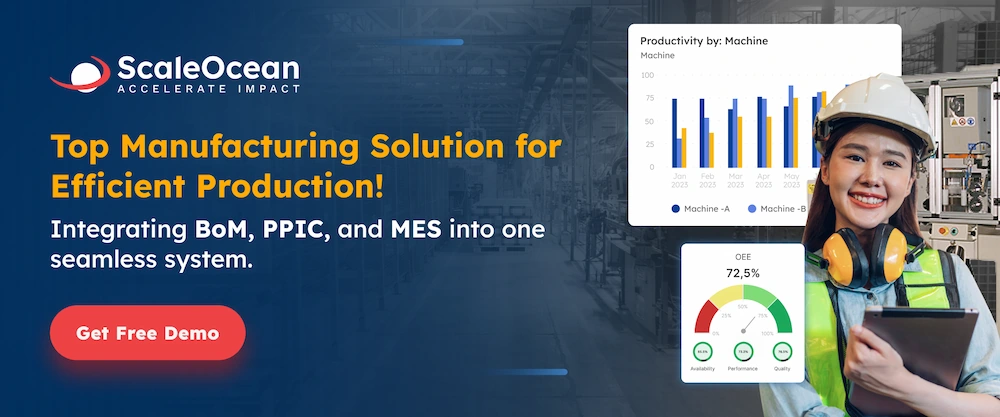
Examples of Manufacturing Overhead
Manufacturing overhead includes all indirect costs associated with the production process that cannot be directly traced to specific products. Examples include factory rent, utilities, equipment depreciation, and maintenance costs. Additionally, indirect labor costs such as wages for supervisors, quality control staff, and maintenance workers are part of overhead.
Supplies like cleaning materials, lubricants, and safety equipment used in the production facility also contribute. Other overhead costs can include insurance, factory security, and taxes on manufacturing property. These costs are essential for maintaining the production environment and must be factored into product pricing for profitability.
How to Reduce your Manufacturing Overhead
Reducing manufacturing overhead costs can significantly improve overall efficiency and profitability. By cutting unnecessary expenses and optimizing resource usage, businesses can lower their production costs. Here are several strategies to consider.
1. Optimize Manufacture Workflow
Streamlining operations involves optimizing production workflows to eliminate bottlenecks and enhance overall efficiency. By regularly assessing each stage of the process, companies can identify wasteful practices and areas of redundancy. Implementing automation and lean manufacturing principles can significantly reduce manual labor costs, improve product flow, and decrease delays, ultimately lowering overhead and boosting productivity.
2. Implement Regular Preventive Maintenance
Regular preventive maintenance is useful for reducing the possibility of equipment failures and costly repairs. Routine inspections and service allow potential faults to be recognized and treated before they become severe concerns. This proactive strategy not only extends the life of machines, but also reduces downtime and manufacturing delays.
3. Repurpose Components from Existing Equipment
Repurposing components from existing equipment can help you save money on future purchases. Instead of discarding outdated parts, companies might discover innovative ways to repurpose them in other processes or equipment. This method minimizes waste, maximizes resource use, and improves overall efficiency, resulting in significant cost savings.
4. Employ an In-House Maintenance Specialist
Hiring an in-house maintenance specialist can reduce the dependency on external contractors. An internal expert can perform timely repairs and maintenance, ensuring that equipment remains in peak functioning order. This technique reduces downtime, improves reaction times, and provides greater control over maintenance plans and costs, ultimately improving cycle time and enhancing production efficiency.
5. Align Employees with Cost-Saving Objectives
Educating and aligning employees with cost-cutting objectives develops an efficient culture. Employees who understand the necessity of decreasing overhead expenses are more likely to help discover and implement cost-cutting solutions. Regular training sessions and workshops can help employees develop a cost-conscious mindset.
6. Strengthen Partnerships with Suppliers
Building strong partnerships with suppliers can lead to better pricing and more favorable terms. Businesses can save money and improve their cash flow management by negotiating bulk discounts and favorable payment arrangements. Maintaining good terms with suppliers also ensures a reliable supply chain and access to high-quality materials.
7. Minimize Dependency on Office Supplies
Reducing reliance on office supplies by going digital can lower overhead costs. Implementing electronic documentation and communication methods not only saves money but also enhances productivity and sustainability. Transitioning to a paperless environment reduces the need for physical storage and streamlines administrative processes.
8. Lease Out Unused Workspace
Leasing out unused space can help to generate revenue and offset overhead costs. Businesses can maximize space efficiency by utilizing underutilized areas within their facility. This strategy generates additional income while improving overall financial stability and resource management.
Also read: What is WIP Management?
Track Manufacturing Costs with ScaleOcean Manufacturing Software
Efficient cost management is crucial for manufacturers to maintain profitability and competitiveness. ScaleOcean Manufacturing Software streamlines cost tracking with an integrated, data-driven approach that connects production and financial metrics. It provides real-time insights, ensuring every stage, from raw material procurement to final product costing, is closely monitored. This enables businesses to identify cost-saving opportunities, optimize production, and minimize inefficiencies to stay competitive. Additionally, the software enhances forecasting and budgeting by leveraging accurate historical data and trends.
Features of ScaleOcean Manufacturing Software for Tracking Costs:
- Real-time Cost Monitoring: Track labor, material, and overhead costs in real time, providing instant insights into cost structures.
- Bill of Materials (BOM) Management: Link raw materials, components, and processes to calculate accurate manufacturing costs.
- Cost Variance Analysis: Compare budgeted vs. actual costs to pinpoint areas for cost control.
- Work Order Cost Tracking: Monitor the cost of individual work orders and batches to identify inefficiencies.
- Integration with Financial Systems: Integrate seamlessly with accounting systems for a unified view of financials and cost reporting.
ScaleOcean provides manufacturers with real-time, accurate data throughout the production lifecycle, allowing for better decision-making to reduce costs and increase profitability. Its comprehensive cost management tools account for all expenses, including materials, labor, and overhead. Seamless integration with other business systems improves visibility and communication, thereby increasing operational efficiency. Furthermore, the software provides valuable insights into cost variances, helping manufacturers refine processes and minimize waste. You can explore its features through a free demo to see how it fits your operations.
Conclusion
Manufacturing overhead is necessary for estimating genuine production costs, although it is frequently underestimated. Managing indirect expenses such as rent, utilities, and maintenance leads to more precise pricing, better planning, and increased profitability. Proper tracking helps companies in properly allocating resources, enhancing output, and improving financial planning, all while eliminating inefficiencies that undermine competitiveness.
With the right tools, overhead management becomes more efficient. ScaleOcean Manufacturing Software offers real-time cost tracking, variance analysis, and financial integration, providing clear visibility into expenses. These insights help businesses refine processes, reduce waste, and boost profitability. Explore how ScaleOcean can support your manufacturing operations with a free demo and discover smarter ways to manage costs.