In today’s competitive manufacturing environment, ensuring high machine availability is critical to maintaining productivity and meeting market demands. In Singapore, the manufacturing sector contributes over 20% to the nation’s GDP, underscoring its significance to the economy. Recent data indicates that Singapore’s manufacturing output increased by 10.6% in December 2024 compared to the previous year, highlighting the sector’s robust performance.
However, such achievements are closely tied to the efficiency and reliability of machinery. Understanding machine availability is essential for manufacturers aiming to minimize downtime and optimize operations. This article discusses the concept of machine availability, its impact on manufacturing efficiency, and strategies for improving it in industrial operations.
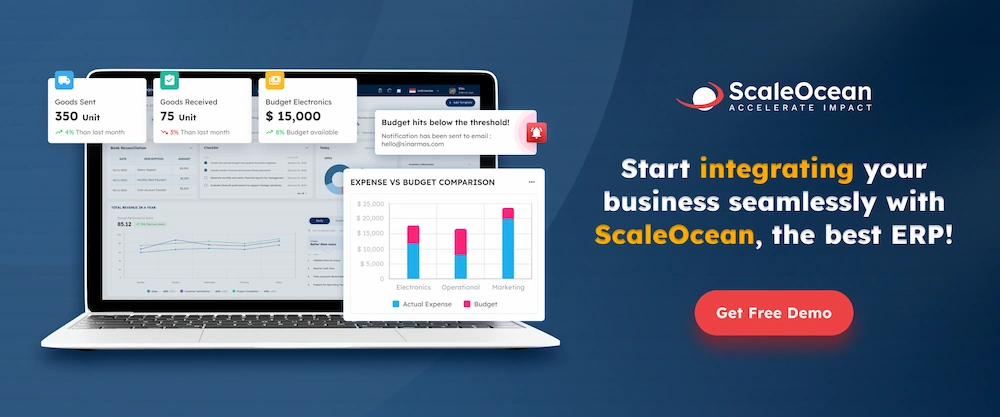
What is Machine Availability?
Machine availability is an important performance metric that measures how well equipment operates in a given timeframe. It represents the percentage of time that machines are available for production without unexpected breakdowns or lengthy maintenance. High availability promotes smooth operations, reduces downtime, and increases overall productivity.
Businesses can improve this metric by implementing preventive maintenance, streamlining workflows, and utilizing advanced monitoring systems. Machine availability in manufacturing and industrial settings has a direct impact on output, cost efficiency, and overall equipment effectiveness (OEE), making it important to achieving operational excellence and maximizing production capacity.
Why is Machine Availability Important?
Ensuring machine availability is important for manufacturing efficiency, impacting production planning and capacity management. High availability minimizes disruptions, while low availability causes delays. Optimizing uptime enhances productivity, streamlines maintenance, and boosts operational effectiveness.
1. Essential for Production Planning
Machine availability ensures a consistent production schedule by minimizing unexpected downtime. Manufacturers rely on precise availability data to effectively allocate resources and meet demand. Without consistent availability, planning becomes unpredictable, resulting in inefficiencies, missed deadlines, and increased operational costs. A properly maintained system keeps production running smoothly and improves overall workflow efficiency.
2. Helps Assess Capacity, Schedules, and Breakdowns
Monitoring machine availability provides insights into production capacity and delivery timelines. It allows businesses to identify potential bottlenecks and anticipate equipment failures before they disrupt operations. By analyzing downtime patterns, companies can optimize scheduling, prevent overloads, and maintain a smooth production flow. Integrating material requirement planning improves scheduling accuracy and resource allocation.
3. Key to Overall Equipment Effectiveness (OEE)
Machine availability is a core component of OEE, alongside performance and quality. High availability means equipment is ready for use, contributing to better productivity. Downtime, whether planned or unplanned, reduces OEE scores, highlighting inefficiencies. Improving availability through proactive maintenance and real-time monitoring enhances equipment utilization and operational efficiency.
4. Higher Availability Reduces Maintenance Needs
Machines with high availability require fewer emergency repairs, lowering unexpected maintenance costs. Preventive maintenance strategies contribute to longer equipment lifespans and more efficient production schedules. Businesses can better allocate maintenance resources by reducing unplanned downtime, avoiding costly disruptions and ensuring a smooth, uninterrupted manufacturing process that improves overall efficiency.
5. Low Availability Leads to Delays and Downtime
Limited machine availability directly impacts production timelines, causing missed deadlines and financial losses. Frequent breakdowns and extended repair times reduce output and disrupt supply chains. Identifying the root causes of low availability, such as inadequate maintenance or outdated equipment, allows businesses to take corrective action to improve reliability and operational continuity.
The Function of Machine Availability
Machine availability is a critical metric in manufacturing, reflecting the proportion of scheduled time that equipment is operational. Understanding its impact helps businesses enhance productivity, streamline maintenance, and optimize resource utilization for sustained operational success.
1. Enhancing Production Planning
Accurate machine availability data enables manufacturers to create realistic production schedules, ensuring efficient resource allocation and timely output. By anticipating potential delays, businesses can adjust plans proactively, minimizing disruptions and improving overall workflow efficiency.
2. Assessing Production Capacity
Monitoring machine availability helps businesses evaluate their actual production capacity, determining whether current machinery can meet demand. This insight allows for strategic decisions on investments in additional equipment or process improvements to support growth.
3. Predicting Maintenance Needs
Analyzing availability trends helps forecast maintenance requirements, reducing unexpected breakdowns. By identifying patterns in downtime, businesses can implement preventive maintenance strategies, extending equipment lifespan and improving operational stability.
4. Improving Overall Equipment Effectiveness (OEE)
Machine availability is a key component of OEE, which measures manufacturing productivity. High availability indicates that equipment is ready for production as planned, contributing positively to OEE scores and highlighting areas for performance improvement.
5. Reducing Operational Costs
Consistently available machines lower emergency repair costs and reduce resource wastage. Well-maintained equipment operates more efficiently, consuming less energy and minimizing unnecessary expenditures, leading to significant cost savings.
6. Enhancing Product Quality
Stable machine availability ensures smooth production processes, which is critical for maintaining high product quality. Unplanned downtimes can disrupt workflows, leading to rushed operations that may compromise quality standards.
7. Facilitating Capacity Planning
Understanding availability trends supports long-term capacity planning. Businesses can make informed decisions on equipment upgrades, replacements, or process adjustments to meet future production demands efficiently.
8. Supporting Continuous Improvement Initiatives
Regular analysis of machine availability provides valuable insights for continuous improvement. Identifying root causes of downtime helps teams implement corrective actions, fostering a proactive approach to operational enhancements and long-term efficiency gains.
How to Calculate Machine Availability?
Machine availability is a crucial metric that evaluates the reliability and efficiency of equipment in manufacturing, production, and industrial environments. It represents the percentage of time a machine is fully operational and capable of performing its intended function. To determine machine availability accurately, businesses can use the following formula:
Machine Availability (%) = (Available Time / Total Time) × 100
Here’s how to break it down:
- Available Time: The time the machine is operational and not under maintenance or repair.
- Total Time: The total time the machine is scheduled to be in operation (e.g., a full shift, day, or week).
For example, if a machine is scheduled to run for 24 hours but experiences 2 hours of downtime, its availability is calculated as:
(22 hours / 24 hours) × 100 = 91.67%
Understanding machine availability helps businesses identify inefficiencies, reduce downtime, and improve productivity. Regularly monitoring this metric ensures optimal equipment performance and supports data-driven decision-making for maintenance and operations.
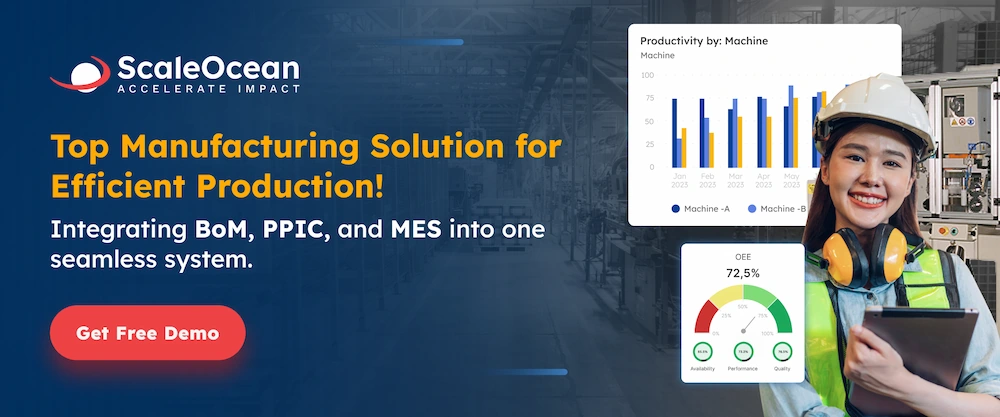
How is Machine Availability Calculated?
Machine availability reflects equipment reliability by calculating the percentage of time it is operational compared to its total scheduled time. Understanding this metric can help businesses increase efficiency, reduce downtime, and optimize resource utilization. Here are the steps to calculate it in three simple steps:
1. Determine Operating Time Ratio
Calculate the ratio of actual operating time to planned operating time. This involves dividing the hours the machine was functional by the total hours it was scheduled to run, providing a clear picture of operational efficiency. A manufacturing accounting system can help track these figures accurately, ensuring precise reporting and analysis.
2. Evaluate Equipment Uptime
Assess the total uptime of all equipment. Uptime refers to the duration machines are actively running without interruptions. Tracking this helps identify reliable equipment and areas needing improvement.
3. Track All Downtime Events
Record every instance of downtime, whether planned (maintenance) or unplanned (breakdowns). Analyzing downtime causes helps implement strategies to minimize disruptions and improve overall machine availability.
Also read: How IoT in Manufacturing Improves Efficiency?
How to Improve Machine Availability
Maximizing machine availability ensures smooth operations, optimal capacity, and minimal downtime. A strategic approach enhances reliability, streamlines workflows, and boosts efficiency. By implementing effective maintenance, optimizing processes, and leveraging technology, businesses can improve uptime. Here are three key strategies:
1. Adopt a Balanced Maintenance Approach
A well-balanced maintenance strategy integrates preventive and predictive maintenance to minimize unexpected failures. Routine inspections, real-time condition monitoring, and data-driven maintenance schedules all contribute to the early detection of potential problems. This proactive approach not only extends equipment life but also reduces maintenance costs and avoids costly disruptions.
2. Optimize Operational Workflows
Inefficient workflows cause unnecessary machine downtime. Standardizing procedures, automating repetitive tasks, and allocating resources efficiently help streamline operations. Clear communication and continuous process improvements enhance machine utilization, reducing idle time and improving production flow. Minimizing inefficiencies also lowers costs of goods sold, boosting profitability and resource efficiency.
3. Utilize ERP Systems for Enhanced Efficiency
Enterprise Resource Planning (ERP) systems integrate maintenance schedules, inventory tracking, and performance monitoring into a centralized platform. Real-time insights allow businesses to anticipate maintenance needs, optimize resource allocation, and automate workflows. By leveraging ERP technology, companies can make informed decisions that enhance equipment reliability and overall operational efficiency.
4. Invest in Employee Training
Employees play an important role for guaranteeing machine availability. Proper training in equipment operation, troubleshooting, and maintenance best practices enables employees to identify and resolve minor issues before they escalate. A properly trained workforce increases equipment reliability, reduces errors, and boosts overall productivity.
5. Monitor Key Performance Indicators (KPIs)
Tracking essential KPIs such as uptime, downtime, and mean time between failures (MTBF) helps businesses assess equipment performance. Regular analysis of these metrics enables early identification of inefficiencies and recurring issues. Companies can use data-driven insights to implement targeted improvements that improve machine availability and lower operational risks.
6. Upgrade Outdated Equipment
Older machinery is more prone to failures and inefficiencies. Replacing or retrofitting old equipment with newer, more energy-efficient models improves reliability and reduces maintenance requirements. Advanced diagnostics, automation, and IoT-enabled monitoring in newer machines increase uptime, ensuring smooth and cost-effective operations.
Also read: What is WIP Management?
The Connection Between Availability and OEE
Availability is a critical component of Overall Equipment Effectiveness (OEE), a metric used to measure manufacturing efficiency. OEE evaluates performance based on three factors including availability, performance, and quality. Availability specifically measures the percentage of time equipment is operational compared to planned production time. High availability ensures that machines are operational when needed, thereby increasing OEE.
However, OEE also considers performance speed and product quality, meaning even with high availability, inefficiencies or defects can lower overall effectiveness. By improving availability through reduced downtime and proactive maintenance, businesses can enhance OEE, driving greater productivity, reduced waste, and improved profitability.
The Difference Between Machine Availability and Machine Reliability
Both machine availability and machine reliability are important for keeping operations running smoothly, but they measure different aspects of equipment performance.
Machine availability refers to how often a machine is ready for use compared to its scheduled runtime. It focuses on reducing downtime, whether planned (maintenance) or unplanned (breakdowns), to keep equipment running when needed. High availability means the machine is well-maintained and efficiently managed.
Machine reliability, on the other hand, measures how consistently a machine operates without failure over time. It looks at how often breakdowns happen and how long they last. A highly reliable machine experiences fewer failures, which helps minimize disruptions and reduce maintenance costs.
Reduce Downtime and Increase Machine Availability with Manufacturing Software ScaleOcean
Unexpected machine downtime can disrupt production and cut into profits. With ScaleOcean Manufacturing Software, you can track, manage, and optimize machine performance to keep operations running smoothly. Our advanced monitoring tools help detect potential issues early, allowing for proactive maintenance and reducing costly breakdowns. By improving machine availability, ScaleOcean ensures your production stays on schedule and operates at peak efficiency. To minimize disruptions and boost uptime with our powerful solution, you may experience it firsthand with a free demo and discover how it enhances your production operations.
Key Features:
- Real-Time Machine Monitoring: Track equipment status, performance, and usage patterns in real time to detect potential issues before they lead to downtime.
- Predictive Maintenance Alerts: Utilize AI-driven insights to predict when maintenance is needed, reducing unexpected breakdowns and costly repairs.
- Automated Work Order Management: Schedule and manage maintenance tasks efficiently, ensuring that servicing is performed at optimal intervals.
- Integrated IoT Connectivity: Connect machines with IoT sensors to gather continuous data and improve operational efficiency.
- Root Cause Analysis (RCA): Identify recurring issues and implement corrective actions to prevent future failures.
With ScaleOcean Manufacturing Software, businesses can achieve higher production efficiency, lower maintenance costs, and improved overall equipment effectiveness (OEE). By reducing unplanned downtime, manufacturers can maintain a steady workflow, fulfill customer demands on time, and optimize resource utilization. Whether you’re looking to scale operations or improve reliability, ScaleOcean provides the tools you need for seamless and efficient manufacturing.
Conclusion
Maximising machine availability is important for maintaining productivity and meeting market demand. In Singapore’s growing manufacturing sector, reliable equipment reduces downtime, enhances production planning, and improves Overall Equipment Effectiveness (OEE). Preventive maintenance, real-time monitoring, and data-driven strategies help sustain efficiency and minimize disruptions.
ScaleOcean Manufacturing Software offers advanced tools for monitoring, predictive maintenance, and workflow automation to help keep operations running smoothly. Manufacturers can avoid costly breakdowns and improve performance by leveraging real-time insights and IoT-driven solutions. Try a free demo today to see how ScaleOcean manufacturing software improves efficiency and long-term success.